GMP/GDP support
At Quality and Vigilance, we work with the sponsor to understand their requirements, priorities and timelines to schedule the audits and provide end-to-end support for the audit and inspection support.
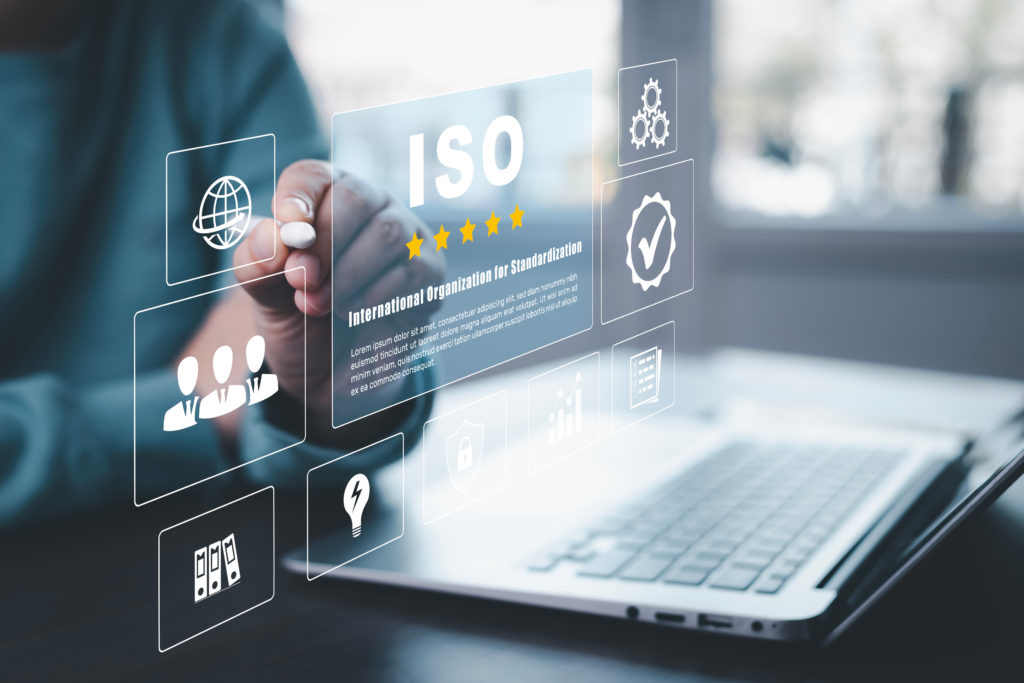
Audits of GMP manufacturing and Test sites
- Drug Product manufacturers (Contract Manufacturing Organisations)
- Medical device manufacturers
- Primary packaging sites (fill sites)
- Secondary packaging
- Contract Test facilities (analytical and microbiological)
Audits of vendors/suppliers
- Raw material suppliers
- Primary packaging material suppliers
- Secondary packaging material suppliers
- Contract storage facilities (stability storage, retain samples)
- Distributors (warehouse facilities)
- Printed packaging/labelling materials
- eQMS vendors
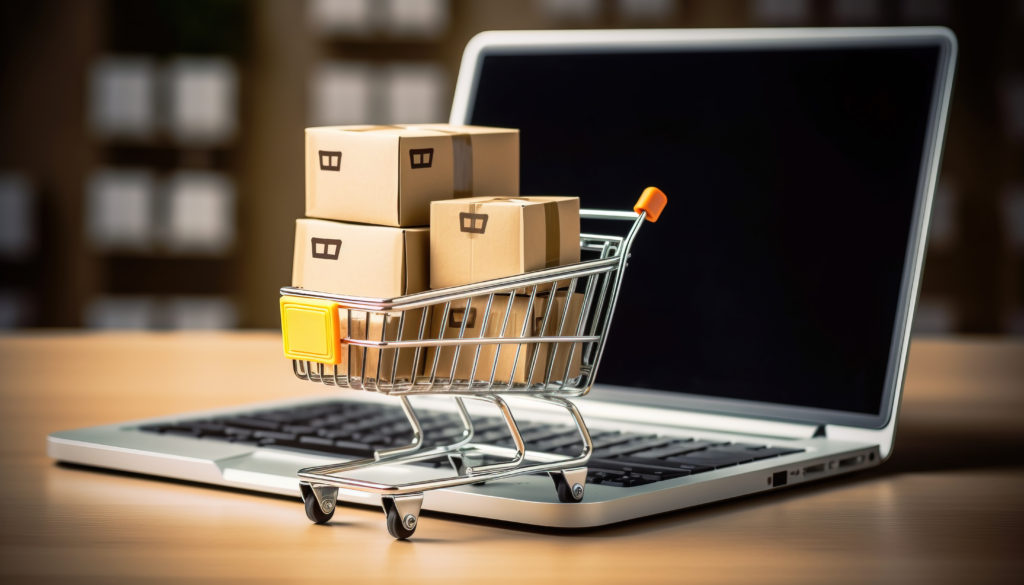
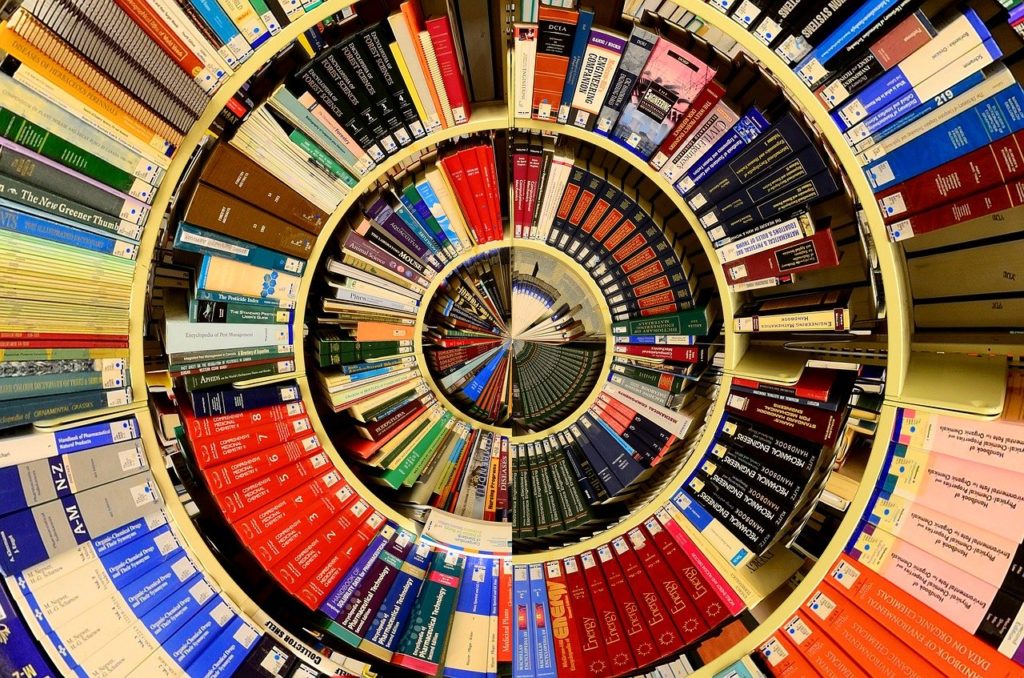
Inspection Readiness
- Mock pre-certification inspections
- Self-inspection and internal audits
- Quality System Audits to 210/211/ICH/EMA requirements
- Identify potential risk and recommendations on mitigate plan.
- Perform gap analyses prior to inspection
Quality Investigations and CAPA
- Coordinate and act with the sites on quality issues, challenges, and queries from operational areas.
- Evaluate concerns on risk-based approach and investigate issues in a methodical way by utilising investigational tools and techniques to determine the root cause and implement Corrective and Preventive Action Plan (CAPA) of the issue.
- We are here to help and support your site to improvise the inspection outcome to back on their feet. Our experts will work with you to address any issues highlighted in the FDA issued 483 and any warning letter observations.
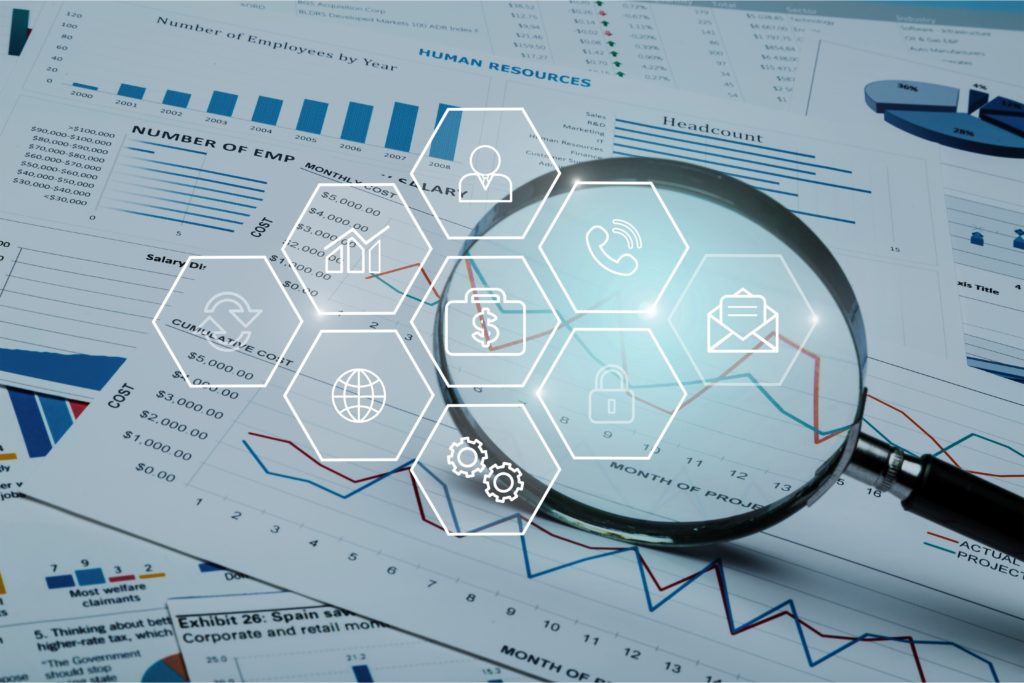
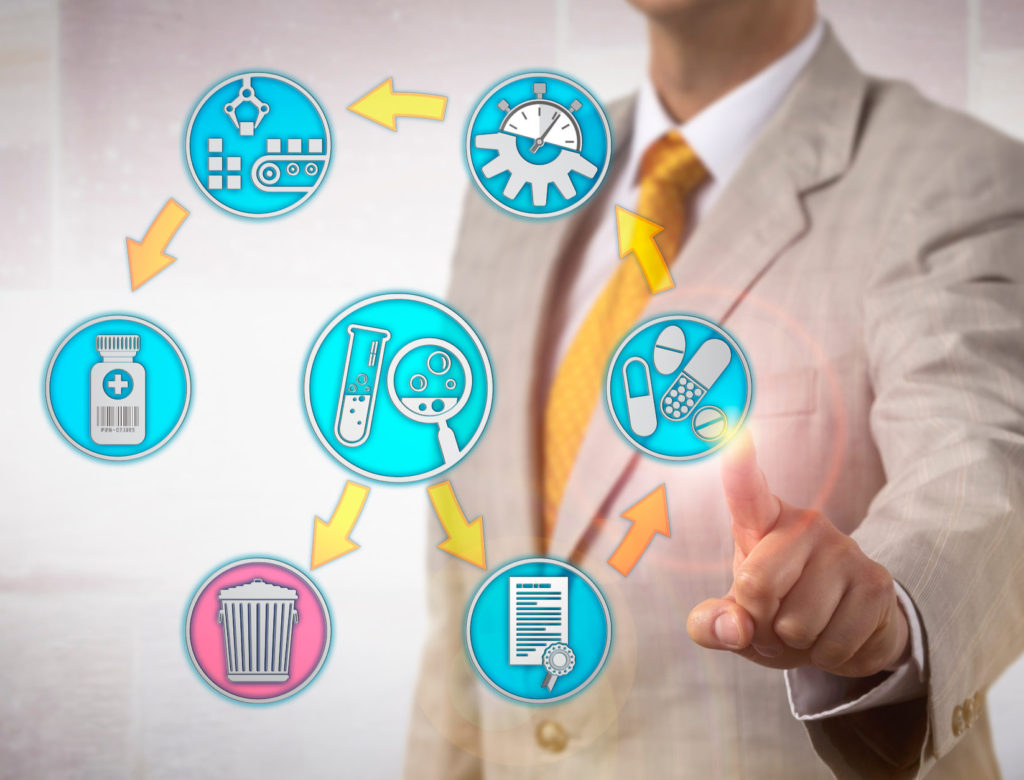
Quality Management System
- Design and develop Quality Management systems
- Support in establishing new GMP systems
- Prepare Standard Operating Procedures
- Build Quality Manual, Site Master File, and Quality Policy
- Implement electronic QMS like Master Control, TrackWise, and Qualio which includes document control, quality events, change control, complaints, and supplier assurance
- Management of Product Quality Complaints
- Management of Product Recall e.g. Initiate recall, communicate to internal stakeholders and regulatory agencies, distributors, clinical trial sites, sponsors, hospitals and inventory reconciliation
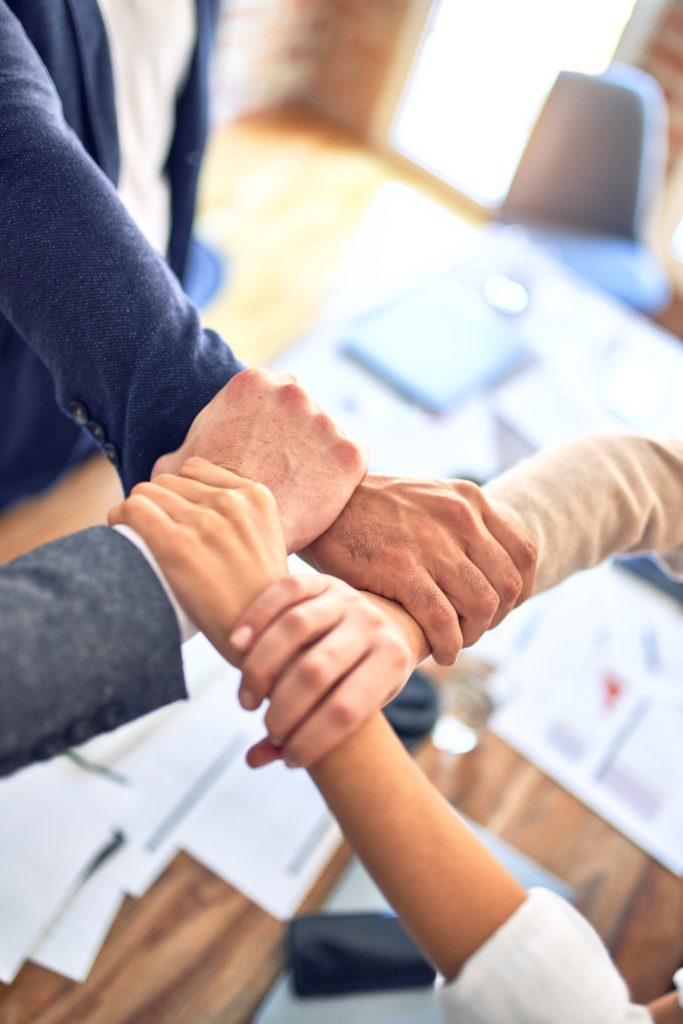
When connected with us, you aren’t fostering growth in the quality of your business alone. We have your back and put in our best to contribute to the growth of your entire systems and processes. So, if you are looking for the right service provider that’ll help you build a good GxP quality presence, we are just a call away.